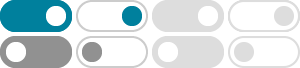
How to Make a Wing - Airbus
Each completed A350 wingset is flown by BelugaXL air transporter to Toulouse operating on a blend of 50% Sustainable Aviation Fuel (SAF), where it is joined to the centre wing box and fuselage during final assembly. Before this production puzzle can …
Airbus A350 - Wikipedia
Airbus adopted a new philosophy for the attachment of the A350's main undercarriage as part of the switch to a composite wing structure. Each main undercarriage leg is attached to the rear wing spar forward and to a gear beam aft, which itself is attached to the wing and the fuselage.
In Photos: How An Airbus A350 Is Built - Simple Flying
Aug 3, 2021 · An A350's assembly begins at Station 59 in the type's dedicated FAL at Airbus's Toulouse factory. This is where pre-installed fuselage modules arrive from Hamburg and Nantes. Here, they are fitted with what are known as 'cabin monuments.'
The Wing Makers - Airbus
Take the wing on the A350, Airbus’ latest widebody. It is reassuringly familiar, yet its swept profile already gives us a glimpse into the future. Like all Airbus aircraft, the A350 wing’s trailing edge can be adapted in flight like a bird's wing to optimise its aerodynamic profile.
Our A350: Building the Wings in Wales - Virgin Atlantic
Opened in 2011 and called the North Factory, the A350 line is the most recent of the Broughton wing production buildings. This world leading wing assembly plant is as big as Wembley Stadium and optimised for energy saving with solar tracking arrays and biomass boilers.
First A350F: Engine pylons and tools are in production - Airbus …
Jan 24, 2025 · The majority of Airbus engine pylons are manufactured at the Saint Eloi site. This titanium component connects the wing to the engine and withstands temperatures from -50° to +600°C. For the A350F version, the MFT in charge of machining and assembly had to take into account the stiffening of the two engine pylons, with reinforced sizing of ...
Airbus Improves Wing Assembly With Mobile Platforms
Apr 6, 2016 · Airbus workers use four inboard and 36 lower-access platforms to build wings horizontally for the A350 XWB airplane. The platforms are maneuvered into place with AGVs. Photo courtesy Bosch Rexroth.
To overcome the challenges of locating and positioning large airframe structures, a measurement assisted assembly system is used. An array of multi-axis positioners lift, move, and align the fuselage and wing structures to guarantee best fit among them. Protecting the large structures during handling is of paramount importance.
The A350 XWB – Advanced Materials and Design - AZoM.com
The Airbus A350 XWB consists of three models-A350-800, A350-900 and A350-1000, each having remarkable flight ranges. Manufacture, assembly and maintenance is optimised by utilising standard parts, systems, airframe materials and powerplants thus ensuring optimal operating efficiency through life.
Final assembly of the first Airbus A350-900 for SWISS begins
Airbus employs a decentralized manufacturing system for the production of the A350. Key components such as wings, fuselage segments, cabin interiors, and computer systems are manufactured at various European sites using state-of-the-art technology. They are then transported to Toulouse, where the final assembly takes place.